Thomas Certo, Gary Brummer and Jacob Lokash | Ankura
In the fast-paced world of construction, delays can pose significant challenges to project success. In this Breaking Down the Walls series, Gary Brummer, a partner at Margie Strub Construction Law LLP, and Jacob Lokash, an associate at the firm, draw upon their extensive legal expertise to explore the complexities of construction delays. They have collaborated with Thomas Certo, a senior director in the Construction Disputes and Advisory Group at Ankura Consulting Group LLC, whose insights into the technical aspects of delay analysis provide a comprehensive perspective on this critical issue.
Together, they simplify the fundamentals of construction delays, providing readers with the necessary tools to proactively identify and assess delays on their own projects. At the end of this six-part series, we will have explored the following topics:
- Delay Claim Basics
- Delay Damages
- Disruption vs. Delay
- Concurrent Delay
- Forensic Schedule Analysis Techniques
- Construction Delay Best Practices
Delay Claims: Understanding the Basics
Construction delay is debated on nearly every construction project, from the smallest renovations to record-breaking megaprojects. Delay leaves various stakeholders asking seemingly simple questions like: Why was the project late? Who caused it? The answers to these questions, however, can be immensely complex.
In Part 1 of this series, we start with analyzing the concept of construction delay and identifying the steps to successfully assert or defend a delay claim. The first step is understanding what delays are.
Exactly What Is “Delay”
The term “delay” in the construction context encompasses more than its ordinary grammatical meaning. Merely observing that an activity has taken place later than planned is only the first piece in a complex puzzle to ultimately determine whether there has been a “delay” to the overall project.
The Society of Construction Law’s Delay and Disruption Protocol1 (SCL Protocol) provides a good starting point in appreciating the meaning of “delay” and the importance of “delay analysis” in the construction context:
In referring to ‘delay’, the Protocol is concerned with time–work activities taking longer than planned. In large part, the focus is on delay to the completion of the works – in other words, critical delay. Hence, ‘delay’ is concerned with an analysis of time. This type of analysis is necessary to support an [extension of time] claim by the Contractor.2
Delay analysis is the process of assessing when and why work started later, ended later, or took longer than planned and how these delays affected the overall project schedule. This ultimately allows parties to assert and defend claims for relief, often in the form of an extension of time (EOT) claim.
Not all delays are treated equally, and consideration must be given to the contractual entitlement to an analyzed delay. There are generally three categories of delay:
- Critical vs. Non-Critical Delay
- Excusable vs. Non-Excusable Delay
- Compensable vs. Non-Compensable Delay
Critical vs. Non-Critical Delay
A delay analysis will most frequently employ the Critical Path Method (CPM), which endeavors to determine the project’s “critical path.” The critical path is the “longest chain of logically connected activities in a project schedule that, if delayed, will delay the end date of a project.”3 Critical path delays are discrete (associated with specific events), happen chronologically (occur over time), and accumulate to the overall project delay (discrete delays add up to the total delay).4
All projects have a critical path, even if one is not readily identifiable from the schedule. The art of identifying critical activities and piecing together the critical path is aided by an understanding of multiple aspects of the project, including (i) the ultimate project deliverable; (ii) the contractor plan and schedule; (iii) contractual requirements for sequencing; (iv) the logical relationship between activities; and (v) the physical or logistical constraints of the project; and (iv) how the project events actually occurred (the “as-built” schedule).
To illustrate a critical path delay, consider the example of a high-rise condominium tower. In order to construct the tower, a logical sequence of work activities is identified in the baseline (“as planned”) schedule. These activities have been simplified and are presented in Figure 1, below.
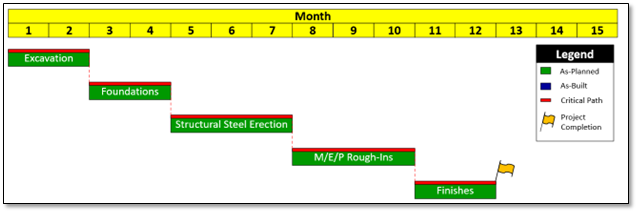
Figure 1 – Example Critical Path
The planned critical path of our condominium tower begins with site excavation, followed by foundations, structural steel erection, mechanical/electrical/plumbing (M/E/P) rough-ins, and finishes. The completion of finishes marks Project Completion. The construction of this condominium tower is planned to take 12 months in total.
We now move four months forward into the construction period, with the status being shown in Figure 2, below.
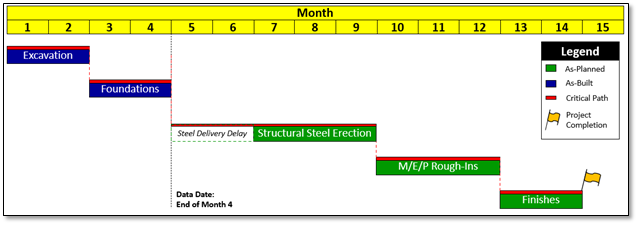
Figure 2 – Example Critical Path Four Months into Construction
Both the excavation and foundation activities have been completed during these first four months, consistent with the planned critical path. However, the construction team has now learned that structural steel deliveries are delayed by two months, meaning that the structural steel installation is also delayed by two months and cannot be installed according to the original plan. Because structural steel erection is on the critical path, this two-month delay to the start of structural steel erection will also result in a two-month delay to Project Completion if structural steel erection and all other activities are completed according to the go-forward plan.
A comparison of the two schedules (the as-planned schedule versus the schedule after four months) shows how the critical steel delivery delay is projected to impact Project Completion, as shown in Figure 3, below.
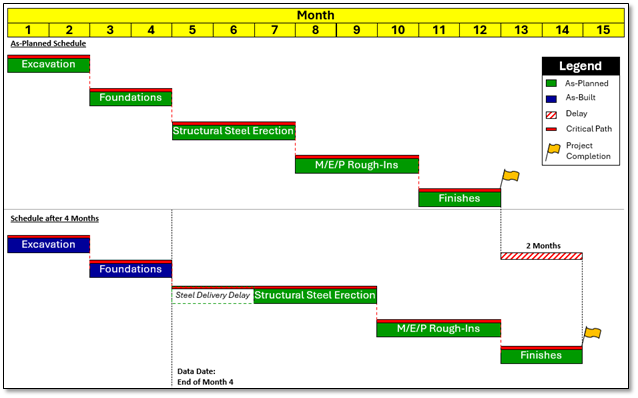
Figure 3 – Example Project Completion Delay from Late Steel Deliveries
Conversely, a non-critical delay would be a delay to an activity that does not impact the completion of the project. These activities can be delayed on their own without impacting the critical path and can be said to have “float.” Using the M/E/P rough-ins from Figure 3 above as an example, any discrete activity delay that does not impact the contractor’s ability to install the M/E/P rough-ins at the beginning of Month 8 is not critical. For example, if the design were received later than planned, but still prior to the start of Month 8, that design delay is not critical because the start of M/E/P rough-ins is controlled by the completion of structural steel erection at the end of Month 7.
For purposes of developing the critical path, non-critical delays are set aside because they do not delay the completion of the project. That is not to say that non-critical delays may not result in a claim – they could; however, the claim would be for the discrete impacts caused by the non-critical delay and not, for example, overall prolongation.
Identifying critical versus non-critical delays is a key component of schedule delay analysis, and often one of the most contested facts during a construction dispute. The fundamentals of schedule analysis and critical path delay identification will be discussed further in Part 5 of this Breaking Down the Walls series, “Forensic Schedule Analysis Techniques.”
Excusable vs. Non-Excusable Delay
Once the critical delays are identified, the next stage of analysis involves determining whether the critical delay events are either excusable or non-excusable. This is a legal analysis that examines both the terms of the contract and the applicable jurisdictional legal principles to determine a party’s entitlement to claim relief for the delay.
Often, excusable delays are delays caused by an unforeseeable event beyond the control of the contractor or subcontractor, also referred to as an “Employer Delay.”5
Classifying a delay as excusable depends on several factors, most importantly the allocation of risk under the contract; however, generally, the following are considered excusable delay events:
- Acts of God (also known as force majeure events), which include various natural disasters, fires, or floods;
- Labor strikes or changes in law, which force the contractor to suspend or delay works;
- Delays caused by the owner or its agent, including but not limited to design changes, failure to provide undisturbed access, or errors and omissions in plans or specifications provided by the owner;
- Differing or concealed site conditions, such as unknown utilities; or
- Lack of action or interference by outside agencies, such as permit approvals.
When a delay is excusable, a contractor is entitled to an EOT, also referred to as an “Employer Risk Event.”6 Thus, a contractor cannot be held in default for a delay that is deemed to be “excusable.” However, an EOT does not necessarily mean that a contractor has an entitlement to additional compensation (this differentiation is addressed in the next section).
A delay is non-excusable when it is driven by a contractor’s action or inaction for an activity that falls within the contractor’s control or responsibility (such as a subcontractor). Again, the contract is typically the controlling source for identifying responsibility for a “Contractor Risk Event.”7 The following are some examples of what are generally considered non-excusable delay events:
- Late performance by subcontractors;
- Late supply of contractor-responsible material;
- Defects and deficiencies; or
- Failure to mobilize sufficient labor or equipment.
These lists are by no means definitive, as a contract or the law of a particular jurisdiction may allocate risk for delays differently. A non-excusable delay will not entitle a contractor to an EOT, which means it is the end of the road in determining whether there may be any entitlement to compensation in the form of delay damages. Identifying a critical path delay as excusable is thus a prerequisite to compensation.
Compensable vs. Non-Compensable Delay
Once it has been determined that there is a critical, excusable delay, the contractor is entitled to an EOT. However, as alluded to earlier, this does not mean that the contractor is entitled to compensation in the form of prolongation costs, often referred to as “delay damages.” Therefore, the final analysis is to determine if a delay is either compensable or non-compensable.
Again, whether a delay is compensable depends primarily on the terms of the contract. In most cases, the contract will specifically identify which delays are non-compensable. For example, a standard form CCDC 2 – Stipulated Price Contract governs compensability as follows:
6.5.1 If the Contractor is delayed in the performance of the Work by an action or omission of the Owner, Consultant, or anyone employed or engaged by them directly or indirectly, contrary to the provisions of the Contract Documents, then the Contract Time shall be extended for such reasonable time as the Consultant may recommend in consultation with the Contractor. The Contractor shall be reimbursed by the Owner for reasonable costs incurred by the Contractor as the result of such delay.
6.5.2 If the Contractor is delayed in the performance of the Work by a stop work order issued by a court or other public authority and providing that such order was not issued as the result of an act or fault of the Contractor or any person employed or engaged by the Contractor directly or indirectly, then the Contract Time shall be extended for such reasonable time as the Consultant may recommend in consultation with the Contractor. The Contractor shall be reimbursed by the Owner for reasonable costs incurred by the Contractor as the result of such delay.
[emphasis added]
GC 6.5.1 and GC 6.5.2 of the CCDC 2 reference delay events which would entitle a contractor to claim compensation, whereas GC 6.5.3 below, serves as an example of delays that, although excusable, are non-compensable:
6.5.3 If the Contractor is delayed in the performance of the Work by:
.1 labour disputes, strikes, lockouts (including lockouts decreed or recommended for its members by a recognized contractors’ association, of which the Contractor is a member or to which the Contractor is otherwise bound),
.2 fire, unusual delay by common carriers or unavoidable casualties,
.3 abnormally adverse weather conditions, or
.4 any cause beyond the Contractor’s control other than one resulting from a default or breach of Contract by the Contractor,
then the Contract Time shall be extended for such reasonable time as the Consultant may recommend in consultation with the Contractor. The extension of time shall not be less than the time lost as the result of the event causing the delay, unless the Contractor agrees to a shorter extension. The Contractor shall not be entitled to payment for costs incurred by such delays unless such delays result from actions by the Owner, Consultant or anyone employed or engaged by them directly or indirectly.
[emphasis added]
The question remains, what is the benefit of an EOT without compensation? An EOT prevents an owner from claiming delay damages against a contractor from the original project completion date through the new EOT date. Many contracts also include a liquidated damages (LDs) clause, which serves as an agreed-upon pre-estimate of damages to cover the costs for each day of delay it takes the contractor to complete the project past the agreed-upon completion date. An EOT provides a contractor with relief from the owner applying LDs, as the agreed-upon completion date is extended by the same amount of time as the contractor’s EOT entitlement.
Whereas a non-compensable EOT is a shield to protect the contractor from a claim for delay damage by the owner, a compensable delay serves as both a sword and shield, allowing the contractor to claim compensation, as well as protecting it from delay damages.
The fundamentals for claiming and defending prolongation costs will be covered in Part 2 of this Breaking Down the Walls series, “Delay Damages.”
The Delay Claim Decision Tree
Each of the above factors can be represented in a form of decision-tree to allow parties to assess the general impacts of a potential delay event:8
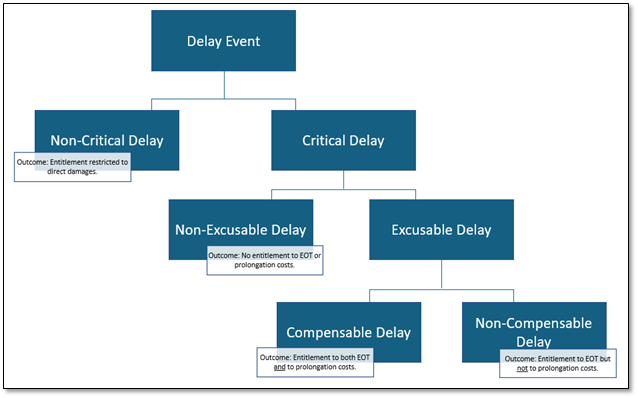
Figure 4 – The Delay Claim Decision Tree
Conclusion
Not all delays are the same, and understanding the difference between various types of delay is only the first step in the process of deciding whether a claim for delay and compensation should be pursued.
Once that decision is made, one must ensure that appropriate professionals are in your corner to provide you with the best chance of success. The first of these is a forensic scheduling expert. The introduction to the AACE Guidelines perfectly sums up the role of forensic scheduling analyst:
Forensic schedule analysis, like many other technical fields, is both a science and an art. As such, it relies upon professional judgment and expert opinion and usually requires many subjective decisions. One of the most important of these decisions is what technical approach should be used to measure or quantify delay and identify the affected activities in order to focus on causation… Professional judgment and expert opinion ultimately rest on subjectivity, but that subjectivity must be based on diligent factual research and analyses whose procedures can be objectified.
Complex projects can have thousands of parallel activities which makes it difficult to isolate the critical path and associated delays. A forensic scheduling expert will have the requisite experience to identify and support the critical path delays.
If a delay is critical, the next step is to consult the contract, which will provide the starting point to determine whether a delay is excusable. Contracts, as we have seen, are written in broad terms. An understanding of legal principles is vital in convincing an owner (or ultimately the trier of fact) that the critical delay was excusable and ultimately compensable.
While this article is written from the perspective of a contractor claiming for delay, the principles apply equally to other stakeholders. An owner or party higher in the construction pyramid can apply the same principles while proactively defending a claim for delay or deciding on appropriate mitigation steps to decrease the impacts of a potential delay.
In Part 2 of this Breaking Down the Walls series, we will delve into the dollars and cents that could be claimed if the delay is compensable.
This article is for informational purposes only and is not intended to constitute legal advice or an opinion on any issues contained therein.
SOURCES
1 2nd edition, February 2017.
2 Paragraph 2, Guidance Part A: Delay, Disruption and Acceleration Concepts, SCL Protocol.
3 Schindler Elevator Corporation v. Walsh Construction Company of Canada, 2021 ONSC 283.
4 Paragraph A of Section 1.5 of AACE® International Recommended Practice No. 29R-03 Forensic Schedule Analysis, April 25, 2011 (“AACE Guideline”).
5 Defined in the SCL Protocol as: “Expression commonly used to describe any delay caused by an Employer Risk Event…”
6 Defined in the SCL Protocol as: “An event or cause of delay or disruption which under the contract is at the risk and responsibility of the Employer.”
7 Defined in the SCL Protocol as: “An event or cause of delay or disruption which under the contract is at the risk and responsibility of the Contractor.”
8 It is important to note, however, that the specific language of the construction contract will ultimately determine liability for delay and entitlement to an EOT.
When one of your cases is in need of a construction expert, estimates, insurance appraisal or umpire services in defect or insurance disputes – please call Advise & Consult, Inc. at 888.684.8305, or email experts@adviseandconsult.net.